CNC Machined Parts Manufacturer: Crafting Excellence in Metal Fabrication
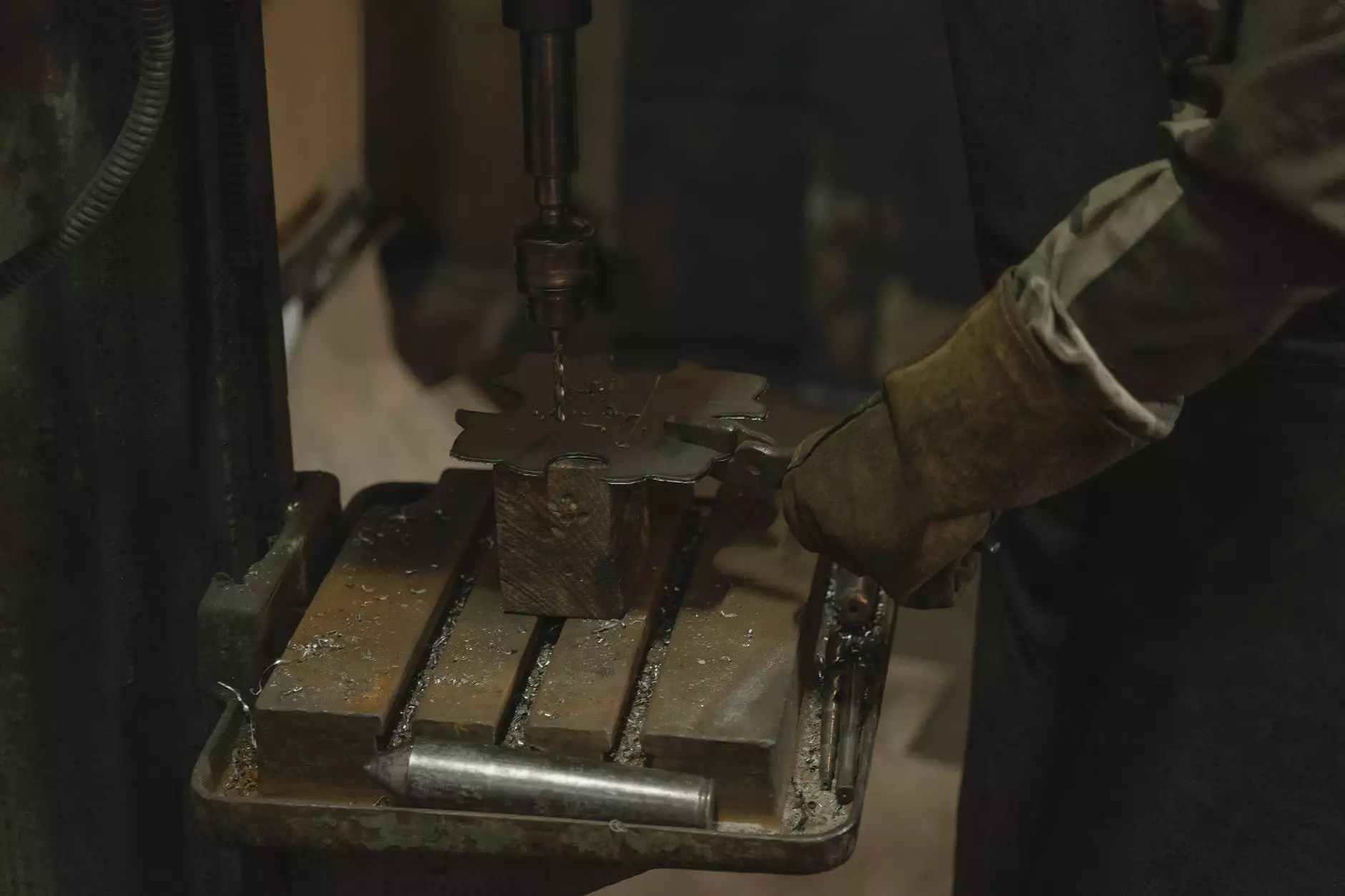
The CNC machined parts manufacturer industry stands at the forefront of modern manufacturing. As businesses increasingly demand precision and efficiency, the role of CNC (Computer Numerical Control) machining becomes ever more critical. Deep Mould, a leading name in the sector, embodies the very essence of quality and innovation in metal fabrication.
Understanding CNC Machining: The Backbone of Precision Engineering
CNC machining is a revolutionary process that utilizes computer-controlled tools to create intricate and precise metal components. Unlike traditional machining methods, which rely heavily on human skill, CNC machining offers consistent quality and unparalleled accuracy. The process involves several key steps:
- Design and Modeling: Engineers create detailed CAD (Computer-Aided Design) models that serve as the blueprint for machining.
- Programming: These CAD models are converted into CNC code, dictating the exact movements and operations of the machinery.
- Machining: The programmed CNC machine executes the operations, cutting, shaping, and finishing the metal parts with precision.
- Quality Control: Rigorous inspection ensures that each part meets strict quality standards.
Why Choose Deep Mould as Your CNC Machined Parts Manufacturer?
Deep Mould is not just a CNC machined parts manufacturer; it is a partner in your success. Here are some compelling reasons to choose us for your metal fabrication needs:
1. Unmatched Quality Standards
At Deep Mould, quality is paramount. We adhere to international quality standards, ensuring that every part we produce is reliable and durable. Our state-of-the-art machinery and skilled technicians work together to deliver products that exceed customer expectations.
2. Tailored Solutions for Diverse Industries
We recognize that different industries have unique requirements. Whether you are in the automotive, aerospace, medical, or electronics sector, Deep Mould provides custom solutions designed to meet specific industry needs. Our flexibility allows us to adapt to changing demands swiftly.
3. Advanced Technology
Deep Mould invests heavily in the latest CNC technology, enabling us to remain competitive in the market. Our machinery is equipped with advanced features, including multi-axis capabilities and automated tool changers, facilitating the production of complex parts with ease.
4. Experienced Team
Our team of experts brings decades of combined experience in the CNC machining field. With a deep understanding of both materials and processes, our technicians ensure that every product is crafted to perfection. Continuous training and learning are integral parts of our culture, keeping us at the cutting edge of technology.
The CNC Machining Process: A Detailed Overview
Understanding the intricacies of the CNC machining process can help businesses appreciate the effort involved in producing quality parts. Here's a breakdown of the process in greater detail:
Step 1: Design and Prototyping
The journey begins with designing the component. Using advanced CAD software, our engineers craft a digital prototype of the part. This stage is critical, as it allows for adjustments and optimizations before moving to production. Prototyping helps us identify any potential issues early on, saving time and resources.
Step 2: CNC Programming
Once the design is finalized, the next step involves CNC programming. This transformation is essential as it translates the CAD model into a language that CNC machines can understand. Our programmers ensure that the instructions are precise, dictating speed, feed rate, tool depth, and more. This meticulous attention to detail guarantees a smooth machining operation.
Step 3: Material Selection
Selecting the right material is crucial for the desired performance and durability of the machined parts. Deep Mould works with a variety of metals, including aluminum, stainless steel, brass, and titanium. Each material has its properties, making it suitable for specific applications. Our experts can advise customers on the best material choices for their projects.
Step 4: Machining Operations
With programming complete and materials at hand, the CNC machine begins the machining process. Different operations include:
- Milling: Cutting and shaping metal by removing material from a rotating tool.
- Turning: Rotating a workpiece against a cutting tool to achieve cylindrical shapes.
- Drilling: Creating holes in the material using rotating drill bits.
- EDM (Electrical Discharge Machining): Using electrical sparks to remove metal and create complex shapes.
Step 5: Finishing
After machining, parts undergo finishing processes to achieve the desired surface quality. This may include sanding, polishing, or coating, enhancing both appearance and functionality.
Step 6: Quality Assurance
Before shipping, every component undergoes rigorous testing and inspection. We utilize advanced measuring tools such as CMM (Coordinate Measuring Machine) to ensure each part meets the specified tolerances. Our commitment to quality assurance means that customers can trust the integrity of every product.
Applications of CNC Machined Parts
CNC machined parts are utilized across a wide range of applications, underlining their versatility and importance in various sectors:
1. Automotive Industry
The automotive sector relies heavily on CNC machined components for manufacturing engine parts, transmission systems, and chassis components. Precision is critical in this industry, where even the smallest error can lead to significant failures.
2. Aerospace Sector
Aerospace components require the highest level of precision and reliability due to their exposure to extreme conditions. CNC machining is indispensable for creating lightweight yet robust parts used in aircraft and spacecraft.
3. Medical Devices
In the medical field, CNC machined parts are essential for producing surgical instruments, implants, and diagnostic equipment. Each piece must adhere to stringent regulatory standards, making quality and precision vital.
4. Consumer Electronics
With the rise of technology, consumer electronics demand high-precision components for devices such as smartphones, laptops, and wearables. CNC machining enables manufacturers to produce intricate designs that enhance functionality.
The Future of CNC Machining
The CNC machining industry is set for significant transformation as technological advancements continue to evolve. Emerging trends include:
1. Automation and Robotics
Integrating robotics into the CNC machining process can significantly enhance productivity and precision. Automated systems are increasingly capable of performing repetitive tasks, allowing human operators to focus on more complex issues.
2. Additive Manufacturing
While CNC machining excels in subtractive manufacturing, the rise of additive manufacturing (3D printing) presents opportunities for hybrid processes, combining the strengths of both techniques for greater efficiency and innovation.
3. Sustainability and Eco-Friendly Practices
As the world leans toward sustainability, CNC manufacturers are exploring eco-friendly materials and lean manufacturing practices. Reducing waste and optimizing resources will be essential for future success.
Why Partner with Deep Mould for Your CNC Machined Parts?
When it comes to selecting a CNC machined parts manufacturer, experience, quality, and reliability are essential. Deep Mould offers:
- Comprehensive Services: From design to delivery, we provide end-to-end solutions tailored to meet your needs.
- Competitive Pricing: We offer competitive rates without compromising on quality, ensuring you get the best value for your investment.
- Rapid Turnaround Times: Our efficient processes and advanced technology enable us to deliver projects on time, helping you stay on schedule.
- Outstanding Customer Support: Our dedicated team is here to assist you every step of the way, ensuring a smooth and hassle-free experience.
Conclusion
As a leading CNC machined parts manufacturer, Deep Mould is committed to delivering the highest quality metal fabrication solutions. Our advanced technology, skilled workforce, and dedication to customer satisfaction position us as your ideal partner in navigating the complexities of modern manufacturing. Whether you're looking for one-off prototypes or large-scale production, we have the capabilities and expertise to meet your needs. Experience the future of CNC machining with Deep Mould—where precision meets excellence.