Hydraulic Tube Fittings Manufacturer: Elevating Industrial Standards
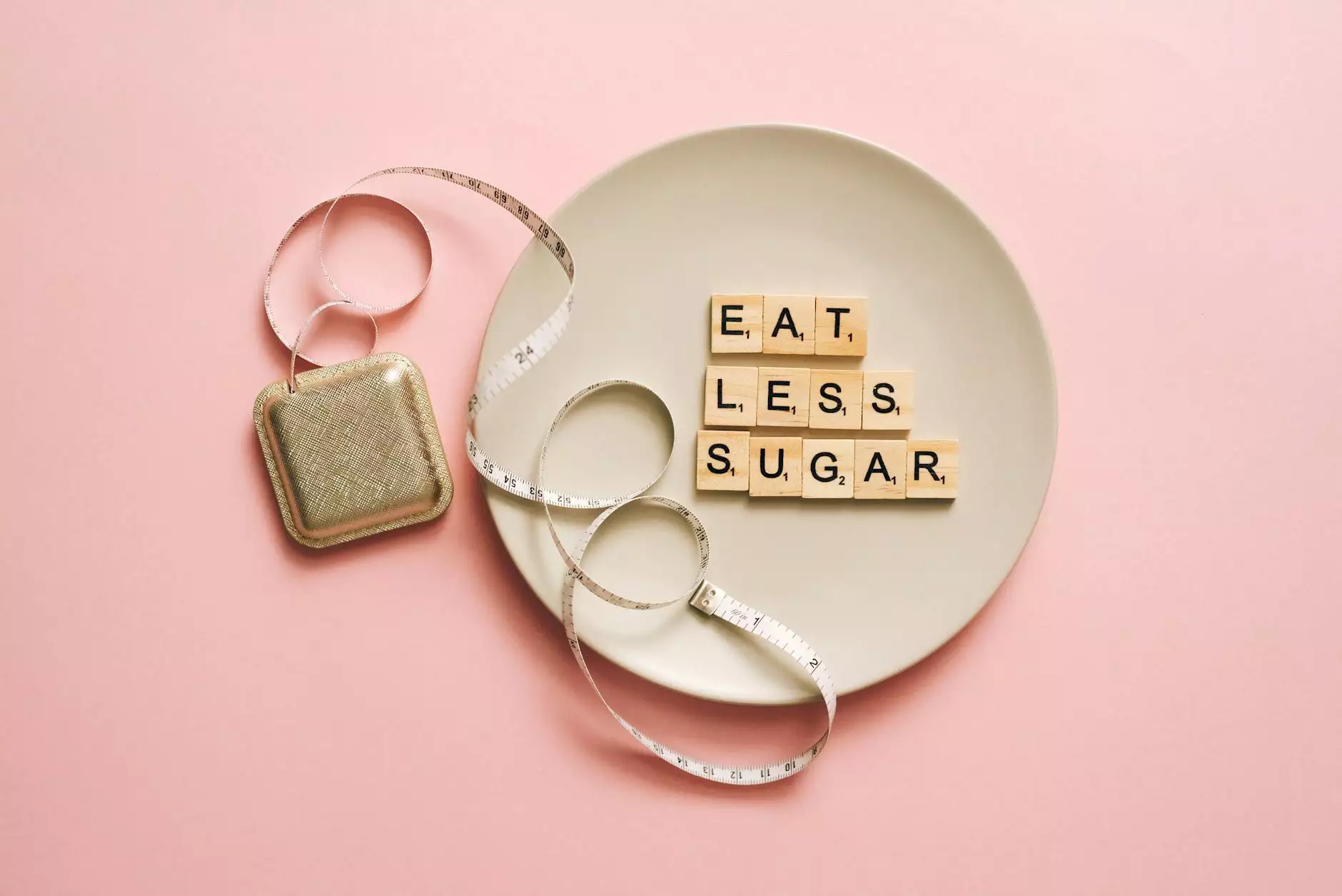
Hydraulic tube fittings play a crucial role in the efficiency and safety of hydraulic systems across various industries. As a premier Hydraulic Tube Fittings Manufacturer, we at Fitsch are committed to producing top-notch fittings that cater to the unique requirements of our clients. This article delves deep into the importance of hydraulic tube fittings, the manufacturing process, types available, and how we ensure quality and reliability.
The Significance of Hydraulic Tube Fittings
In modern hydraulic systems, the role of hydraulic tube fittings cannot be understated. They serve as the crucial link that connects various components, allowing for the efficient transfer of hydraulic fluid under high pressure. Here are some key reasons why these fittings are essential:
- Pressure Management: Hydraulic fittings are designed to withstand high pressures, ensuring that fluid does not leak and systems operate efficiently.
- Safety: High-quality fittings minimize the risk of leaks, which can lead to dangerous situations and costly downtime.
- Versatility: They accommodate various tube sizes and materials, making them suitable for diverse applications.
Types of Hydraulic Tube Fittings We Offer
At Fitsch, we understand that different applications require different types of fittings. As a trusted Hydraulic Tube Fittings Manufacturer, we take pride in our extensive range of hydraulic tube fittings, including:
1. Compression Fittings
Compression fittings are widely used for connecting tubes. They provide a strong, leak-proof seal, making them ideal for medium to high-pressure applications.
2. Flared Fittings
These fittings feature a conical flare that ensures a secure connection. They are often used in automotive and aviation applications.
3. Welded Fittings
Welded fittings are permanently attached and provide exceptional strength and durability, making them suitable for high-pressure environments.
4. Push-On Fittings
Easy to install, push-on fittings require no tools. They are perfect for low-pressure applications and provide flexibility in design.
The Manufacturing Process: Ensuring Quality at Every Step
As a leading Hydraulic Tube Fittings Manufacturer, maintaining high standards in quality is paramount. Here's a look at our comprehensive manufacturing process:
Step 1: Material Selection
We begin by selecting high-quality materials that meet industry standards. Stainless steel, brass, and carbon steel are commonly used due to their strength and corrosion resistance.
Step 2: Precision Machining
Next, our advanced CNC machinery meticulously shapes and sizes each fitting to ensure precise dimensions. This step is crucial for the proper function of the fitting.
Step 3: Surface Treatment
All fittings undergo surface treatment processes, such as plating or coating, to enhance durability and resistance to environmental factors.
Step 4: Quality Control
We perform rigorous quality checks at every stage of production. This includes pressure testing and dimensional analysis to ensure reliability and safety.
Why Choose Fitsch as Your Hydraulic Tube Fittings Manufacturer?
Here are several reasons why Fitsch stands out as a reliable manufacturer in the hydraulic fitting market:
- Expertise: With years of experience in the industry, our team possesses in-depth knowledge of hydraulic systems and fittings.
- Innovation: We invest heavily in R&D to stay ahead of market trends, ensuring that we offer cutting-edge solutions to our customers.
- Custom Solutions: We recognize that every project is unique. Therefore, we offer tailored solutions to meet the specific needs of our clients.
- Competitive Pricing: Our efficient manufacturing process allows us to maintain competitive prices without compromising quality.
- Customer Support: Our commitment to customer satisfaction is paramount. We provide comprehensive support and guidance throughout the purchasing process.
Applications of Hydraulic Tube Fittings
The versatility of hydraulic tube fittings makes them applicable in a multitude of industries. Some common applications include:
1. Automotive
Hydraulic fittings are used in braking systems, power steering, and transmission lines.
2. Construction
Heavy machinery relies on hydraulic systems, and robust fittings ensure these machines operate effectively.
3. Manufacturing
Hydraulic systems in industrial machinery depend on quality fittings for optimal performance.
4. Aerospace
In aviation, reliable hydraulic fittings are critical for safety and performance in aircraft systems.
Maintenance Tips for Hydraulic Tube Fittings
To ensure the longevity and effective performance of hydraulic tube fittings, consider the following maintenance tips:
- Regular Inspections: Periodically check fittings for any signs of wear or damage, especially in high-pressure systems.
- Cleaning: Maintain a clean environment to prevent contamination, which can lead to system failure.
- Proper Installation: Always follow manufacturer guidelines during installation to ensure fittings are secured properly.
- Monitor Pressure: Keep an eye on the pressure levels within the hydraulic system to identify potential issues early.
Conclusion: Partner with Fitsch for Superior Hydraulic Solutions
As a prominent Hydraulic Tube Fittings Manufacturer, Fitsch is dedicated to providing quality products that enhance the efficiency and safety of hydraulic systems. With our extensive range of fittings for sale, cutting-edge manufacturing processes, and unwavering commitment to customer satisfaction, we stand ready to meet all your hydraulic fitting needs. Explore our offerings at fitsch.cn and experience the difference in quality and service today.
Hydraulic Tube Fittings Manufacturer